Packaging 101: The Complete Guide
- Packaging 101
- Types of Packaging
- Aseptic Packaging
- Blister Packaging
- Biodegradable Packaging
- Bulk Packaging
- Carbon Neutral Packaging
- Circular Packaging
- Clamshell Packaging
- Compostable Packaging
- Cornstarch Packaging
- Corrugated Packaging
- Discreet Packaging
- Ecommerce Packaging
- Flexible Packaging
- Frustration Free Packaging
- Retail Packaging
- Secondary Packaging
- Smart Packaging
- Sustainable Packaging
- What is a PR Package?
- What is a Poly Mailer?
- Packaging Design Ideas
- AI Packaging Design
- Bakery Packaging Ideas
- Bath Bomb Packaging Ideas
- Bath Salt Packaging Ideas
- Body Butter Packaging Ideas
- Body Oil Packaging Ideas
- Body Scrub Packaging Ideas
- Brownie Packaging Ideas
- Cake Packaging Ideas
- Cake Pop Packaging Ideas
- Candle Packaging Ideas
- Candy Packaging Ideas
- Canva Packaging Design
- Chocolate Packaging Ideas
- Cinnamon Roll Packaging Ideas
- Clothing Packaging Ideas
- Coaster Packaging Ideas
- Coffee Bag Design Ideas
- Cookie Packaging Ideas
- Cosmetics Packaging Design
- Cotton Candy Packaging Ideas
- Cupcake Packaging Ideas
- DIY Packaging Ideas
- Dog Treat Packaging Ideas
- Food Packaging Ideas
- Empanada Packaging Ideas
- Etsy Packaging Ideas
- French Fries Packaging Ideas
- Frozen Food Packaging Ideas
- Hair Extension Packaging Ideas
- Handbag Packaging Ideas
- Jewelry Packaging Ideas
- Keychain Packaging Ideas
- Lash Packaging Ideas
- Lip Gloss Packaging Ideas
- Macaron Packaging Ideas
- Minimalist Packaging Ideas
- Mug Packaging Ideas
- New Employee Welcome Kit Ideas
- Packaging Colors
- Packaging Inserts Ideas
- Packaging Logo Design
- Packaging Typography
- Perfume Box Design Ideas
- Pizza Box Design Ideas
- Popcorn Packaging Ideas
- Scarf Packaging Ideas
- Skincare Packaging Design Ideas
- Soap Packaging Ideas
- Sock Packaging Ideas
- Sticker Packaging Ideas
- Sunglass Packaging Ideas
- Sustainable Packaging Ideas
- Tea Packaging Ideas
- Wax Melt Packaging Ideas
- Weed Packaging Ideas
- T-Shirt Packaging Ideas
- Wine Packaging Design Ideas
- What is a Packaging Engineer?
- Types of Packaging Materials
- Chipboard vs Cardboard
- Compostable Packaging Materials
- Alternatives to Plastic Packaging
- Edible Packaging Materials
- Food Packaging Materials
- Are Poly Mailers Recyclable?
- How to Recycle Cardboard Boxes
- How to Recycle Packaging Materials
- Medical Device Packaging Materials
- Mono Material Packaging
- Pharmaceutical Packaging Materials
- Plastic Food Packaging
- Protective Packaging Materials
- Reusing Packaging Materials
- Types of Packaging Foam
- Void Fill Packaging
- What is Chipboard?
- What is Kraft Paper?
- Offset vs Digital Printing
- RGB vs CMYK Printing
- Screen Printing vs Digital Printing
- Screen Printing vs Sublimation
- What is a Dieline in Packaging?
- What is Die Cutting?
- What is Digital Printing?
- What is Flexographic Printing?
- What is Glassine Paper?
- What is Offset Printing?
- What is Spot UV Printing?
- Why is 300 DPI Good for Printing?
- How to Estimate Shipping Costs
- How to Pack Glass for Shipping
- How to Mail a Bubble Mailer
- How to Make a Shipping Label
- How To Measure Box Dimensions and Sizes
- How to Ship Alcohol
- How to Ship Artwork
- How to Ship Books
- How to Ship a Cake
- How to Ship Candles
- How to Ship Chocolate
- How to Ship Clothes
- How to Ship Cookies
- How to Ship Food
- How to Ship a Hat
- How to Ship Jewelry
- How to Ship a Laptop
- How to Ship Perfume
- How to Ship a PC
- How to Ship Perishable Food
- How to Ship Plants
- How to Ship Shoes
- How to Ship Vinyl Records
- Packaging Symbols
- Shipping Large Items
- What is a Delivery Exception?
- What is Shipping Insurance?
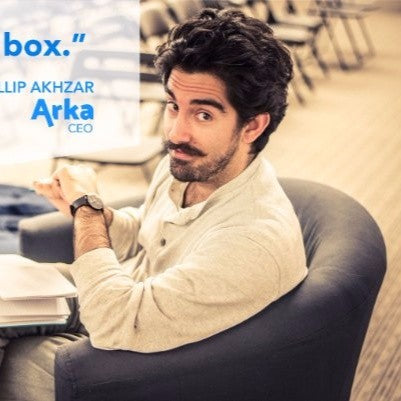
Discover Phillip Akhzar’s journey, the Founder and CEO of Arka, bringing 16 years of expertise in packaging and supply chain logistics. Read more on Arka.
How Does Flexographic Printing Work? 4 Components
Flexographic printing, a cutting-edge method, employs pliable relief plates to imprint ink onto diverse surfaces. Its versatility renders it a favored option across various uses such as packaging, labels, and newspapers.
The procedure encompasses several integral elements, each contributing to the accuracy and efficiency of the flexographic printing process.
• Imprinting Plates: The core of flexographic printing lies in the printing plates. Typically crafted from rubber or polymer, these plates bear the elevated image or text for printing. The relief surface facilitates efficient ink transfer, ensuring precise and sharp impressions on the final output.
• Inks and Solvents: The selection of inks and solvents is pivotal for achieving the desired print quality. Flexographic printing employs swiftly drying liquid inks that adhere well to various surfaces. Solvents enhance ink fluidity and rapid drying, augmenting the printing speed.
• Anilox Rollers: Anilox rollers play a crucial role in regulating the quantity of ink transferred to the printing plates. These rollers possess engraved cells that meter the ink before application to the plates. This controlled ink delivery guarantees consistent and accurate printing, even on diverse materials.
• Printing Surfaces: The adaptability of flexographic printing is apparent in its capacity to print on an assortment of surfaces, ranging from paper and cardboard to plastic and foil. This flexibility establishes it as the preferred choice for industries where distinct materials necessitate diverse printing solutions.
Advantages and Challenges of Flexographic Printing
Flexographic printing, also referred to as flexo printing, is a versatile and extensively employed technique in the realm of printing. This method employs pliable relief plates and is esteemed for its adaptability across different substrates. But what is flexographic printing used for, and how does flexographic printing work? Let's delve into the advantages and challenges of this printing process.
Advantages of Flexographic Printing
Here are the key benefits of this printing method:
• Ensuring Print Consistency: A pivotal strength of flexographic printing lies in its capability to maintain consistent print quality over extensive print runs. This reliability proves indispensable for industries necessitating standardized and high-quality packaging, such as those in food and beverage or pharmaceutical sectors.
• Cost-Effectiveness in Large Runs: Notably, flexographic printing distinguishes itself through cost-effectiveness, particularly in managing substantial print volumes. The process enables efficient production, making it the preferred choice for businesses with significant printing requirements, resulting in substantial long-term cost savings.
• Environmental Considerations: Flexographic printing takes center stage within the ambit of environmental awareness. Using water-based inks emerges as a noteworthy eco-friendly attribute, diminishing environmental impact compared to conventional solvent-based inks. Additionally, the process minimizes waste, aligning seamlessly with sustainability objectives.
Challenges of Flexographic Printing
Let’s explore the main challenges of using this printing method:
• Setup Time: Despite its efficiency in extensive print runs, flexographic printing often demands a relatively longer setup time in comparison to alternative printing methods. This may pose a drawback for businesses with smaller print quantities or those seeking swift turnaround times.
• Initial Costs: The investment in flexographic printing equipment entails higher initial costs, presenting a potential hurdle for smaller enterprises or startups. Nevertheless, the cost-effectiveness of managing large print runs can offset this initial investment over time.
• Color Limitations: Flexographic printing encounters restrictions concerning color options when juxtaposed with certain digital printing methods. The attainment of a diverse spectrum of colors can prove challenging, impacting the flexibility of design choices for specific applications.
Environmental Considerations of Flexographic Printing
• Water-Based Inks: A notable environmental facet of flexographic printing revolves around the use of water-based inks. This choice diminishes the emission of volatile organic compounds (VOCs) linked to solvent-based inks, contributing to a cleaner and healthier working environment.
• Reduced Waste: The flexographic printing process minimizes waste generation during printing. Its adeptness in efficiently printing on diverse substrates, coupled with precise printing plates, contributes to reduced material wastage, fostering sustainable and eco-friendly printing practices.
What is Flexographic Printing Used for? Key Applications
Flexographic printing is a versatile and efficient printing method widely employed for various applications; now, let's delve into its key applications and explore the diverse industries that benefit from this efficient printing process.
Packaging Excellence
Flexographic printing is crucial in the packaging industry. It offers a cost-effective and high-speed solution; it excels in printing on various packaging materials, from cardboard to plastic, making it a preferred choice for industries like food, beverage and consumer goods.
Labeling Precision
In label printing, flexography stands out for its ability to produce high-quality labels rapidly; it accommodates diverse materials, ensuring sharp and precise images. This makes it ideal for product branding, logistics, and label information display.
Flexible Packaging
Flexographic printing is extensively used in flexible packaging, including pouches, bags, and wrappers for snacks and consumer goods; its flexibility allows for eye-catching designs while maintaining the durability needed for flexible materials.
Newspapers and Magazines
In print media, flexographic printing is notable in newspaper and magazine production; its speed and efficiency meet the demands of high-volume printing. While offset and digital printing have roles, flexography remains a reliable option for large-scale newspaper runs and specific magazine formats.
Flexographic Printing vs. Other Printing Methods
In the ever-evolving realm of printing, diverse methods vie for prominence in shaping packaging, labels and more. Among these contenders, flexographic printing emerges as an exceptionally versatile player. Let's explore the comparisons between flexo and two other noteworthy printing techniques: offset printing and gravure printing.
Flexo vs. Offset Printing
• Flexographic Printing: Flexo relies on flexible relief plates and rapid-drying inks. This adaptable method suits a wide array of materials, encompassing paper, plastic and labels. Recognized for its flexibility, flexo stands as a favored choice for packaging, labels and newspapers.
• Offset Printing: In contrast, offset printing utilizes a flat image carrier and a succession of rollers to transfer ink to a rubber blanket before reaching the printing surface. Renowned for producing high-quality images, offset printing may be less efficient for certain substrates. It excels in applications like book printing, magazines, and sophisticated marketing materials.
Flexo vs. Gravure Printing
• Flexographic Printing: Flexo and gravure printing share commonalities. However, flexo employs a flexible relief plate and a rotary press, enhancing its adaptability for shorter print runs and diverse substrates. Flexo proves advantageous for intricate designs and finds suitability in food packaging materials, labels and corrugated materials.
• Gravure Printing: Conversely, gravure printing utilizes engraved cylinders to transfer ink directly onto the substrate. While excelling in long print runs and delivering high-quality images, gravure may be less cost-effective for short production cycles. Gravure finds favor in extensive printing projects like magazines, catalogs and decorative laminates.
Final Thoughts
Flexographic printing emerges as the linchpin in the packaging revolution, offering unparalleled versatility and efficiency.
As companies seek innovative solutions for their packaging needs, Arka stands out with its expertise and commitment, offering tailored solutions to elevate brands through innovative and impactful packaging designs.
Explore our top-notch custom shipping boxes and mailer boxes – let's craft your ideal packaging together.
FAQs on Flexographic Printing
What role does flexography play in personalized packaging?
Flexography allows for adaptable personalization in packaging, easily adjusting to different materials such as paper, plastic, and labels, making it ideal for personalized packaging with unique designs, texts, or graphics.
How has technology impacted flexographic printing?
Technology has positively impacted flexographic printing, elevating its flexibility for intricate designs and enhancing efficiency in managing a range of substrates. Technology contributes to eco-friendly practices, improved color management, and overall modernization of the flexographic printing process.